HISTORY | Chapter 7 Driving on the wave of ukulele
The 1920s was a golden age in which Martin quickly expanded. At that time, ukulele became the new favorite of American public leisure culture and entertainment. However, Martin’s first ukulele was not as popular as it was supposed to be. The ukulele looked too much like a guitar. They used too many bracing structures, especially on the panels, and they were still spruce brackets. The overweight volume structure made this ukulele sound dull, so it was not welcomed by the buying community at the time.
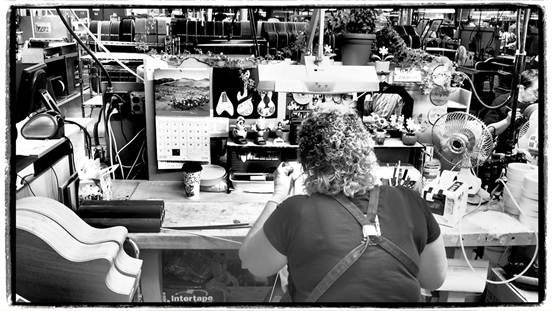
Recognizing the design flaws of the first ukulele, Martin was not discouraged, but continued to develop a more suitable ukulele. By reducing the amount of sound beams and replacing mahogany materials, Martin’s ukulele quickly blended into the wave of the time and occupied a considerable market share. At that time, in order to meet the excess demand, Martin had to expand his factory at that time by more than doubled. In 1920, the total guitar production was 1,361. However, the output of ukulele was not counted. Martin III conservatively estimated that the ukulele production at that time should be more than twice the guitar production.
For the internal organizational structure of the company, Frank Martin appointed Martin III for production forecasting and control, while his brother Herbert Keller Martin was responsible for the sales process. This division of labor began very smoothly at first, until his brother Herbert Keller Martin died suddenly in 1927. With the death of his brother, Martin III has increasingly participated in the company’s sales activities, and constantly went to the country to carry out sales activities.
In the decade of the 1920s, Martin’s sales performance grew at a good rate every year. By 1928, the annual production of guitar had reached 5,215 per year, almost five times that of 1920. But with the advent of the Great Depression of 1929, the national economic downturn forced Martin’s strategy to move toward survival. The massive unemployment and the bankruptcy of credit institutions have made guitar sales a challenge.
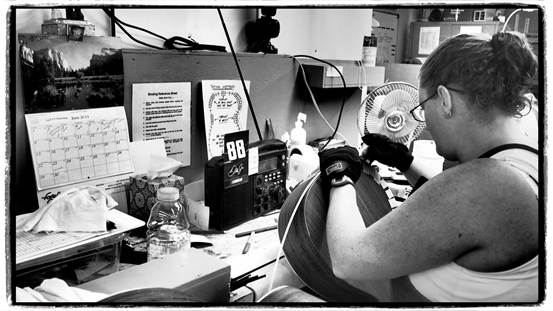
Between 1929 and 1931, guitar sales plummeted to half. For the bleak living environment, Martin had to make a decision to lower the salary and change the working system to three days a week. The factory also carried out production changes, they began to produce violin parts and wooden jewelry. In fact, this is just to make the craftsmen in the factory busy.
In fact, the Martin factory has never made the determination to spend time in these areas. “We always worry that other production will affect the concentration of our guitar production.” Martin III stressed, “We were involved in some other production during the Great Depression, but we were not very happy to do it. It was entirely helpless.”
In order to stimulate and grow the increasingly sluggish sales, Martin launched an activity to stimulate production development. During this period, the company put a lot of new designs on the production line, replacing existing products, trying to find a way to overcome the sluggish sales by trying fresh products. Although some products have to face a short-lived fate, there are also some designs that have become the capital of the company, such as the famous Dreadnought body and the invention of the 14-fret joint to the neck.
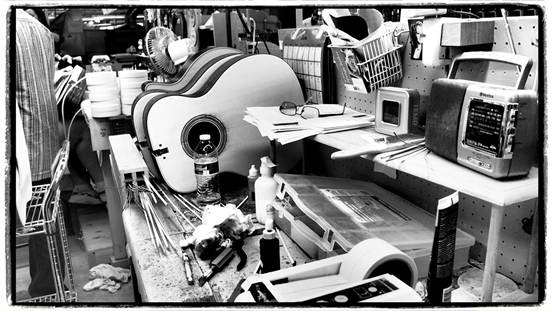
HISTORY | Chapter 8 Martin Innovation
According to Martin III, the combination of the 14-fret joint neck was introduced in late 1929. Prior to this, the guitar basically used a combination of 12 necks. Over time, a well-known plucked banjo master, Perry Bechtel suggested that Frank Henry Martin make a 14-fret guitar. Bechtel believes that a longer neck can greatly broaden the guitar’s range and make the guitar a guitar a more perfect instrument. After accepting his suggestion, Martin released a new guitar, which was the 14th fret “Orchestra Model” at the time.
Unexpectedly, the 14-fret joint neck guitar was very popular with the people at that time, and eventually became the production standard of the Martin production line and replaced the original neck technology. This standard has since become the universal standard for the American guitar industry.
The name “Dreadnought” is quite a bit of a head. Its name comes from the British invincible warships of the First World War. This shape of the body has become the symbol of Martin. The original D-type guitar was designed by Frank Martin and Harry Hunt (the manager of the famous instrumentalist Chas. H. Diston Co. at the time known as Philadelphia, Boston and New York). At the time, the two speculated that the huge body could give the guitar a better bass and resonance response, which would be very suitable for singers. The first D-type guitar was produced in 1916 and sold under the name “Oliver Diston & Co., Boston, New York”. At the time, not many people could accept such a guitar. Because there were very few musicians who used guitars to sing at the time. The solo musicians also think that the D-type bass is too exaggerated. However, with the prosperity of folk music, the sales of D-type guitars have entered a period of rapid rise. Until now, this guitar type is still the top priority of Martin. And almost all other guitar manufacturers and production individuals have used this body as a benchmark for design.
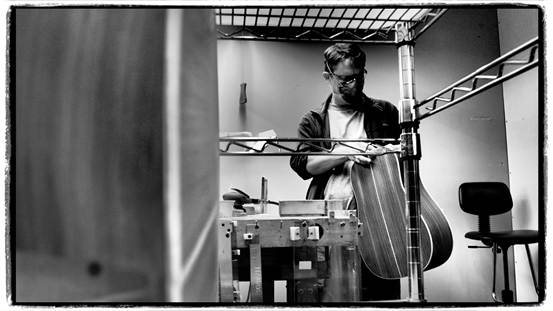
Frank Martin died in 1948 at the age of 81. Martin III has inherited the business of his ancestors, and Martin has continued its legendary quality and brilliance. The post-war prosperity, accompanied by the flourishing of folk music, made the period from 1948 to 1970 the flourishing period of Martin. However, the excess demand made Martin’s production line overwhelmed, so that in the early years of the 1960s, Martin’s orders would even be delayed for three years! However, Martin’s order postponement appears to be so envious of the industry. However, Martin III said that they were very embarrassed at the time. He said, “Some people come to the music store with hundreds of dollars to find a Martin guitar. He wanted to buy it instead of three years. We can get it later. Our lack of capacity at the time was actually not conducive to the relationship with customers and distributors.
The son of III participated in the family business in 1955. His name inherited the name of his late uncle and grandfather. His name was Frank Herbert Martin. The father and son jointly decided to build a larger production plant. Although the original North Street factory has been a few high-rise buildings after several generations of development, it still cannot achieve greater production capacity. “The factory building in North Street was not the most suitable production address at the time. In fact, the longevity of our Martin family members is somewhat related to the stairs of these factories every day. Haha, I can’t bear it.” III said at the time.
The production model of the new plant on Sycamore Street is slightly different from that of the old factory in North Street. Handmade is still a trait that Martin is proud of. However, the new plant canceled the design of the multi-storey building in pursuit of higher production efficiency, and all production activities were completed on the same floor. So the production line process can become smoother, which has to be said to be the best of both worlds, both to improve efficiency without losing quality.
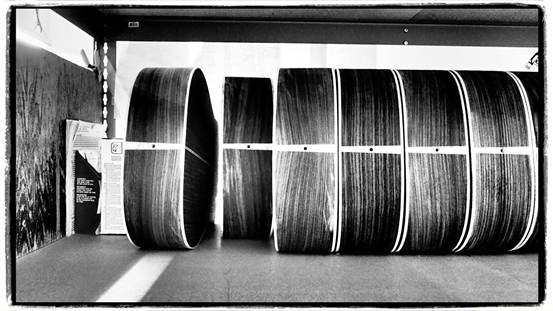
Under the leadership of Frank Herbert Martin, who is no less than his father’s ability, Martin began the stage of merger and expansion of the market. In 1970, Martin acquired the Vega Banjo workshop in Boston and a few months later merged the Fibes Drum Company (which once produced a special fiberglass drum). The larger merger was the acquisition of the Darco String Company in 1970. The former owner of the company was the famous old John D’Addario and his son. Another big deal in the 1970s was the acquisition of Swedish A.B. Herman Carlson Levin, which used to produce classical guitars and some steel wire models. Within a few years, Vega, Levin and Fibes were sold again by Martin. However, the Martin & Darco strings are retained as part of the company’s internal components.